MIG versus TIG
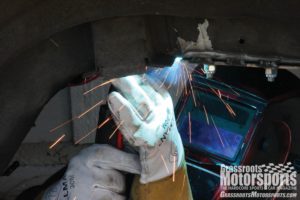
We’ve spent a lot of time discussing welding skills and technique in this magazine, but maybe it’s time to back up and start at the beginning: How do you decide what kind of welder to use in the first place?
Sure, the skills and techniques we’ve covered apply to all types of welding, but we’ve generally assumed that our readers are most familiar with MIG welding. The MIG approach has become nearly ubiquitous thanks to the availability of relatively inexpensive, high-quality machines from numerous manufacturers.
However, more and more members of the grassroots community are getting their hands on TIG welders. A new wave of lower-cost equipment and a bevy of craigslist ads hawking used machines have given enthusiasts another affordable way to weld.
If you sit around and bench race welders with your friends, one of them will quickly proclaim that TIG is better than MIG. Is that true? Well, let us put forth this proposition: As with most of life’s big questions, the answer is, “It depends.” The two types of welders operate differently, and each one has its advantages and disadvantages. We’ll let you make the final call based on your needs.
Hard or Soft?
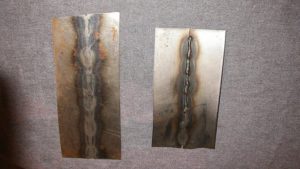
MIG and TIG welds feature different levels of hardness—technically called malleability. The piece on the left was TIG welded and hammered. The one the right was MIG welded and hammered, but cracked.
Let’s get right to it with some quick definitions. MIG stands for metal inert gas, while TIG stands for tungsten inert gas. Further, the M and T give us important information about each method’s heat source. Let’s dig into that subject next.
In the case of MIG welding, the heat source is the consumable wire. The wire and its arc heat the surrounding (base) metal, melting it together into a fused and welded joint.
With TIG welding, the heat source is the tungsten-tipped torch. The arc from the torch heats the surrounding metal, and then the consumable rod is melted in, forming the fused and welded joint.
Doesn’t sound like these two welders are all that different, right? Turns out they really are: Where the heat comes from and, more importantly, where the heat goes, can significantly affect weld quality.
With MIG welding, the heat starts at the weld joint and moves to the base metal. With TIG welding, the heat starts at the base metal and moves to the weld joint.
Another big factor is how the weld cools. A MIG weld cools much faster than a TIG weld. That’s because the base metal surrounding it serves as a heat sink that quickly sucks the heat from the MIG joint. A TIG joint, on the other hand, cools relatively slowly because the base metal is already very hot—and that means no heat sink effect.
A couple parts of this story will prompt the engineers to chime in with angry emails about our grassroots explanations of deeper science. Here’s their first opportunity to do so: Time to discuss the strength differences between these two types of welds.
Most people understand that heat treating metal usually involves heating it and then cooling it, often rapidly. When metal is heat treated, it often becomes harder, which implies—and means—more strength. This strength is often measured as tensile strength.
While high tensile strength is the real deal, it does have a couple side effects: increased brittleness and reduced malleability. Harder metal truly is stronger—but it’s only stronger until it breaks. Plus, sometimes brittleness is a bigger problem than low tensile strength.
Let’s apply this to how MIG and TIG weld joints cool. It turns out that a MIG weld joint becomes very hard and very brittle due to its fast cooling. Conversely, a TIG joint’s slower cooling leaves it softer and more malleable.
Clean or Dirty?
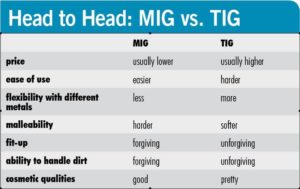
There’s more to these two types of welds than their strength and malleability. A large factor in the quality of a weld is the joint’s cleanliness, and this is another area where MIG and TIG welding are quite different.
Most people understand that the inert gas used in MIG and TIG welding plays a huge part in keeping the joint clean. However, they’re overlooking the role of heat.
Both machines circulate inert gas—usually argon, CO2 or a mix of both—around the weld joint to keep it from becoming contaminated with dirty ambient air. This process works very well, but the gas shouldn’t get all the credit. It turns out that heat can really help clean a weld joint, too, and that’s where MIG offers an advantage.
Think about a self-cleaning oven. It works by running at a very high temperature, burning the crud off the racks and interior surfaces. The heat concentrated at the MIG joint has a similar effect on the base metal, improving the quality of the weld.
You’ll remember that we strongly advocate cleaning weld joints thoroughly before welding. In fact, “You can’t weld dirt” is one of our welding mantras.
While buying a MIG welder won’t get you out of cleaning duties, sometimes it’s difficult to remove all of the grime. In these cases, MIG welding is your best bet. Maybe TIG isn’t always better than MIG after all. See how it depends?
Steel or Aluminum?
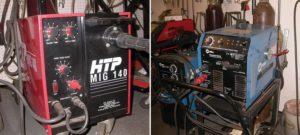
When it comes to home welding, many people gravitate toward MIG units (left). A TIG unit (right) doesn’t take up much more space in the shop, but the welding process is a bit more involved.
Now let’s go a little deeper into welding operation and theory. Engineers, here’s your second chance to scoff at our generalizations or grab your pitchforks.
We’ve talked about how heat affects the weld joint, and we’ve talked about where the heat is applied—at the joint or at the surrounding metal. It turns out that the polarity of the welder also affects where the heat ends up.
When welding steel, both MIG and TIG machines use DC current. There tends to be more heat on the positive side of an electrical circuit, and a MIG welder’s torch and wire typically handle that end of things; its ground wire is usually set to negative. This setup makes the MIG weld joint hotter and the base metal cooler.
A TIG welder’s polarity is the opposite. Its torch is set to negative and the ground is set to positive, which means heat travels into the base metal. Here’s the rule of thumb: With a MIG weld, two-thirds of the heat is in the weld joint and one-third is in the base metal. With a TIG weld, the inverse is true: Two-thirds of the heat is in the base metal and one-third is in the weld joint.
Let’s look at the TIG welding process a bit more. It uses DC current for steel, but it switches to AC current to tackle aluminum. Why the special treatment? Because aluminum is much more sensitive to contamination than steel. It’s also much more likely to crack.
Aluminum requires a welding process that can handle dirt well (like MIG) and create a less brittle weld joint (like TIG). TIG welding with AC current offers a set of compromises that make it more suitable for the job. Let’s dive even deeper into the process. An AC circuit reverses polarity 60 times per second on common household or industrial current sources. They don’t call it alternating current for nothing.
With TIG, the ideal setup for welding has the torch negatively charged and the base metal positively charged. The ideal setup for cleaning is when the polarity is reversed. Since AC current causes the polarity to switch constantly and rapidly, a single TIG welder can handle both the welding and cleaning processes. The result: a quality weld joint.
As a side note, more advanced TIG welders allow the user to adjust the AC process: You can lengthen the negative grounding wavelength to boost the cleaning capabilities, or lengthen the positive grounding wavelength for faster and more powerful welding.
So, what about welding aluminum with MIG? While it is becoming more common and practical to use specially equipped MIG welders for aluminum, TIG still tends to hold the advantage and is more flexible in most cases. This specific topic really warrants its own story, so keep your eyes peeled for that in a future GRM.
Simple or Complex?
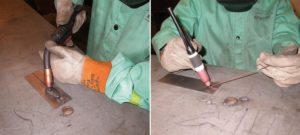
MIG (left) and TIG (right) machines both require the operator to use different techniques, but MIG welding is a bit easier.
If MIG welding is like throwing a ball, TIG welding is like juggling three of them. Guess which one is more difficult to master.
MIG welding can be a one-handed, point-and-shoot operation. You set the welder, pull the trigger, and off you go. With TIG welding, you’ve got to handle three different operations at once. One hand holds the torch and the other hand feeds the rod. Meanwhile, your foot is on the current pedal, and the harder you push, the more current (heat) you put into the weld.
As with juggling, these three factors must be in sync with one another or you’ll drop the ball and mess up the weld. So, this is another difference between MIG and TIG: It takes more time and practice to become proficient at TIG welding.
While that may make TIG seem less appealing, its complexity is actually a benefit. Good welding is about good control, and with a TIG welder you can dynamically control a lot more of the welding process.
With MIG, you set your current and wire speed before welding. After that, you don’t have to worry about them—but you can’t adjust them while you weld, either. TIG welding, on the other hand, allows you to make adjustments on the fly. If you need a little more heat, just press the pedal a little further. If you need a little less, back off a bit. More filler? Feed the rod faster. And so on.
TIG welders offer a level of flexibility that can greatly improve the quality of a weld. (Note: There are high-end MIG welders on the market that let you adjust these parameters as you go, but they’re generally out of reach for most enthusiasts.)
Another practical difference between these two welders involves prep work: MIG welding is more forgiving when it comes to the fit-up of the joint. Since TIG welding requires heating the base metal and then melting the rod, the base metal components need to fit together very tightly so they can be evenly heated and thus evenly melt the rod. If there’s an air gap, the weld will often fail. On the other hand, since a MIG welder’s heat source is the filler wire, it’s not only more forgiving to the base metal, but it can also fill air gaps to some extent.
Fast or Slow?
Whether you’re welding on the job or at home, time is usually money. MIG and TIG units operate at different paces, both before and during the welding process.
Assuming you have a higher-end MIG welder that can handle aluminum, converting it from its steel setting requires some work. Typically this means changing the shielding gas, the wire, the welder polarity (often with some disassembly of the welder) and even the liner or the whole welding torch assembly. Setting up a TIG welder for aluminum is usually as easy as flipping a switch from DC to AC and using a different rod.
However, MIG welding is typically a speedier operation than TIG welding. Since the wire feeds automatically and the heat gets in the weld joint faster, MIG welding is generally a timesaver.
We usually figure that MIG welding is about two to three times faster—that is, it will take two to three times as long to lay a 12-inch bead with TIG than MIG. That extra time may not matter to everyone, but especially in production environments, MIG can offer a distinct advantage.
See, It Really Does Depend
Finally, there’s the cosmetic factor. Even the staunchest defenders of metal inert gas will admit that TIG welds look better than MIG welds. Sure, MIG welds can look nice, but TIG welds can approach art. That stacked-coins look produced by a well-executed TIG weld is what most welders are after, especially on exposed welds.
Compared to the lumpier and less graceful look of the MIG weld, TIG work generally wins any beauty contest. So, is TIG better than MIG? It’s certainly got some advantages, but so does MIG. We hate to say it, but the answer really depends. At least now you have the information to make the decision for yourself.
Which is the best for us? How’s this for an answer: We’ve got both types in our shop, and we pick the best one for the operation at hand.